
The efficiency of your manufacturing processes is crucial to your company’s success. With greater efficiency, you can take on more clients, process more material and improve your warehouse’s safety. As a result of all these benefits, many companies put in the time and effort to consider how they can make their manufacturing processes more efficient.
As you look to improve your manufacturing processes, you may want to learn more about the common problems warehouses face and review tips to improve the efficiency of various processes. There are also key pieces of equipment you can invest in for greater production.
Jump To Sections:
- Problems Facing Efficiency in the Warehouse
- How to Improve Efficiency in the Warehouse
- Benefits of Efficiency
- Equipment to Improve Efficiency
Problems Facing Efficiency in the Warehouse
There are a few challenges warehouses regularly face when they look to improve their efficiency. A warehouse may be unorganized and filled with staff who haven’t been trained appropriately. Additionally, many warehouses haven’t built a collaborative culture, which leads to a lack of proper communication in the workplace.
Warehouses may also rely on equipment that is prone to breaking down or outdated equipment that is unable to handle material at high speeds. A company may not prioritize regular equipment maintenance, resulting in downtime and lowered efficiency when a piece of equipment breaks down.
In addition, companies regularly run into the problem of setting unrealistic expectations for their employees without taking a look at their workflow and evaluating what they can actually expect. Warehouses that haven’t standardized their processes also suffer from a lack of efficiency in their company’s workflow.
How to Improve Efficiency in the Warehouse
To address common warehouse efficiency challenges, you can practice a few tips designed to get the most out of your staff and equipment. Learn more about how to improve warehouse efficiency below:
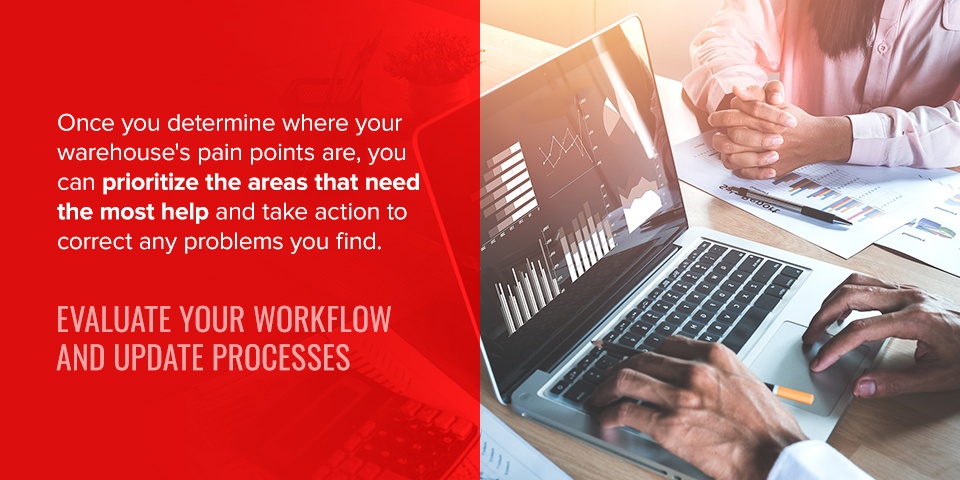
1. Evaluate Your Workflow and Update Processes
Improving your warehouse’s efficiency starts with examining the challenges your workflow regularly encounters. It’s often a good idea to have your workflow evaluation include the analysis of processes, technology and staff. You may also want to get a sense of your company’s resources, procedures and communication tools.
Once you determine where your warehouse’s pain points are, you can prioritize the areas that need the most help and take action to correct any problems you find. With these priorities in place, you can design and implement plans to address areas needing improvement. These plans may include adjusting your budget, moving resources around or obtaining certain certifications. After you begin implementing fixes and new practices, it’s best practice to track and keep data on these changes to see if they’re effective.
2. Prioritize Employee Training
Employee training can assist with your warehouse’s productivity significantly. Well-trained employees know how to operate equipment, maintain safety protocols and keep their production high throughout the day. Companies that want to reduce mistakes and improve their efficiency make employee training a priority. Prioritizing employee training starts with regularly scheduling learning sessions for your employees, whether to train new employees or provide a refresher to seasoned staff members.
Effective training can keep employees updated on using the latest technology in your warehouse. Since new technology brings greater capabilities and different steps employees must follow, training employees for the changes is a must. Good training can also prepare employees to handle multiple processes. By learning more about your warehouse’s different processes, employees can fill in for others when needed and better troubleshoot issues when problems arise.
3. Standardize Processes
Another way you can increase your warehouse’s efficiency is to make sure everyone knows what they should be doing and how they should be doing it. Having a standard plan for how employees conduct tasks reduces errors, inefficiencies and injuries arising from allowing staff to go about their work without clear direction. Standardizing your process also ensures your employees use an efficient workflow.
One of the easiest ways to implement new processes is by creating a checklist or listing the steps to a process in a document. You can place the checklist in all the relevant workstations to make it visible to workers and remind them how they’re supposed to complete a task.
4. Organize Your Warehouse
If you want to know how to increase warehouse productivity, you’ll likely want to consider how organized your warehouse is. Companies that lack proper organization on the warehouse floor often see a dip in productivity due to difficulties finding needed materials or navigating an area with obstructions on the ground. To ensure you have clear pathways throughout your warehouse, you can adjust the layout into a more space-efficient configuration.
An organized warehouse keeps everything in the right place. Your parts, documents, equipment and tools should all have a place where they’re stored and where employees can find them easily. With your staff knowing where all needed items are, it’s less likely they may have long periods of downtime as they search for something.
5. Foster a Collaborative Environment
Your warehouse can be more efficient when everyone is on the same page and is working together. Teams who communicate with one another are more likely to engage in the most efficient practices and avoid mistakes. Good communication starts with managers taking the time to speak with team members one-on-one and ensure they feel comfortable in their role.
If you want to know how to improve employee well-being, a collaborative environment is a great place to start. Letting staff know you’re interested in listening if they have any suggestions for improvement is one way to encourage collaboration. Hearing out staff members who have ideas for making their work more efficient can improve your processes and make team members feel more valued. It’s crucial to have a clear chain of command and instructions for how to make comments, complaints or suggestions to management.
6. Set Realistic Expectations
Setting unreachable production expectations can leave your staff discouraged and your clients dissatisfied as you fail to meet deadlines. Take time to evaluate all your processes and determine a manageable amount of time it should take to complete them. When you set these realistic goals, it’s likely your workers will become more productive. Employees won’t be overwhelmed from having an insurmountable workload, and they won’t have to deal with injuries from working too fast.
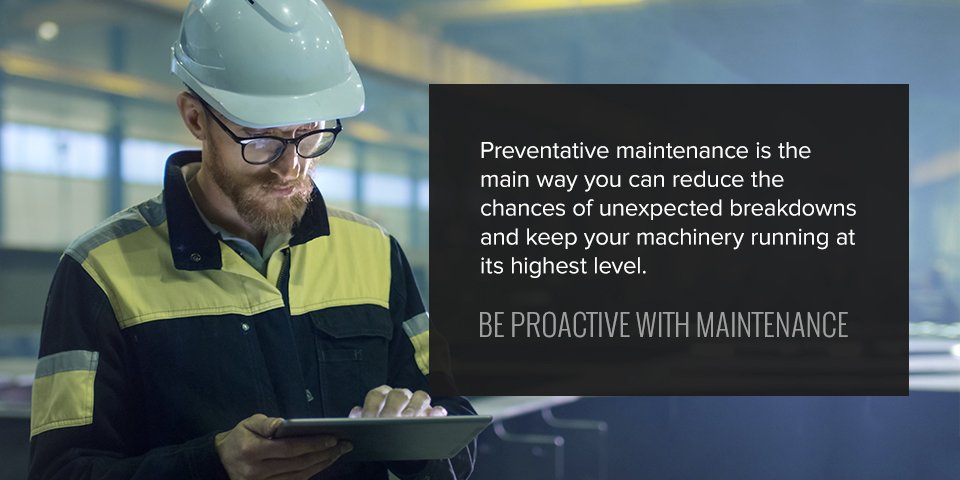
7. Be Proactive With Maintenance
Equipment breakdowns can slow your processes significantly and create more downtime for staff as they wait for replacement parts and repairs to be completed. Preventative maintenance is the main way you can reduce the chances of unexpected breakdowns and keep your machinery running at its highest level. Regular equipment inspections and maintenance should be scheduled to ensure maintenance remains a priority.
For an even better handle on your equipment, you can train employees to recognize common issues with machinery so they can warn management before a problem gets worse. Staff can also be trained to troubleshoot issues to find the cause of an error and take the appropriate action after finding the cause.
8. Invest in More Efficient Equipment
Having the right equipment for your workers is one of the biggest factors in improving the efficiency of your workplace. When workers have to complete their tasks by hand, it will take longer than a machine designed to complete the task. The right machinery can speed up your tasks significantly, leading to more materials processed per day and greater productivity overall.
You can also invest in automated equipment that doesn’t need users to operate it. This more advanced equipment can handle tasks even faster than those operated manually while freeing up your staff for other tasks. You can find equipment designed to handle your materials quickly and with as little chance of user error as possible, leading to increased efficiency.
Benefits of Efficiency
Increasing your efficiency has several advantages you may not have considered. For instance, increased efficiency can lead to more clients, greater worker safety and better customer service. Below you can find some of the primary benefits of improving efficiency at your warehouse:
- Take on more clients: One of the primary advantages of improving your warehouse’s efficiency is that it increases the amount of work you can get done in a day. This greater output means you can take on more clients and projects, helping your business expand and raise profits.
- Improve customer service: When you hit your deadlines and get products to customers on time, you can have much more satisfied customers. A more efficient warehouse also means you’re better organized, making it easier for your support staff to find answers to customer questions.
- Increase safety: Knowing how to improve warehouse safety is directly tied to increasing your warehouse’s efficiency with new equipment. Efficient equipment reduces the need for manual labor to handle heavy material. Having to lift and adjust heavy materials manually can lead to injuries. With equipment designed to handle material, your staff will no longer have to handle heavy products by hand, increasing their safety and productivity.
- Reduce costs: There are often expensive costs associated with inefficient practices, such as those related to having to devote more labor to a task and lost income from not meeting client expectations. With more efficient practices in place, your company can lower your costs and bring in more income by speeding up key processes.
- Free up staff: When you implement efficient practices at your warehouse, you’ll likely reduce how many staff members you have to devote to a task or shorten the amount of time it takes workers to finish their responsibilities. Reducing the amount of labor required to finish a task can save costs related to paying staff and help your warehouse be more productive.
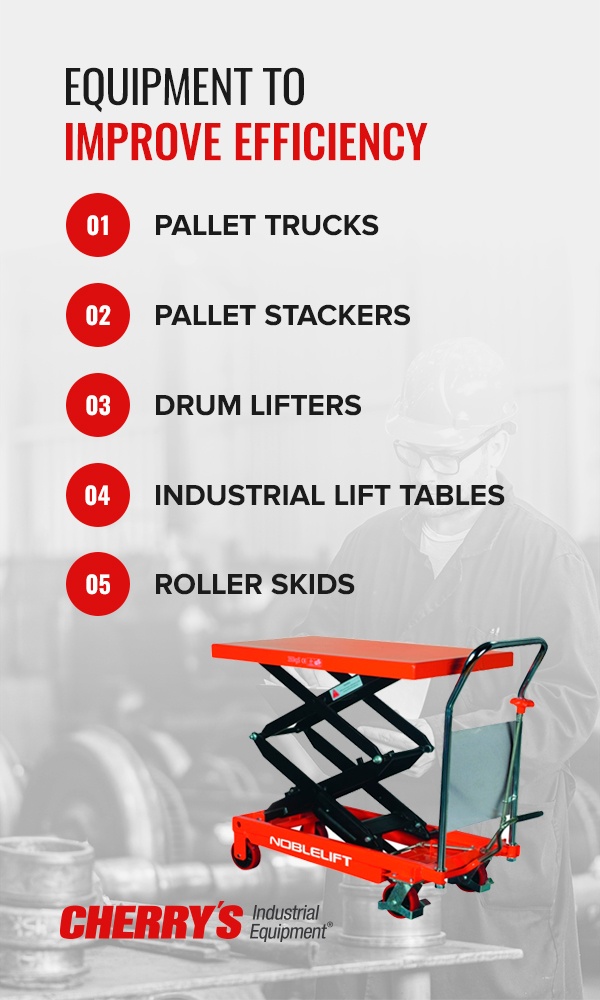
Equipment to Improve Efficiency
Equipment to Improve Efficiency
The benefits of labor-saving equipment are unmatched when you look to improve the efficiency of your warehouse. As such, you might be interested in investing in high-quality equipment designed to improve manufacturing processes. Review some of the primary pieces of equipment you can add to your warehouse to improve your efficiency:
- Pallet trucks: You likely handle pallets in your warehouse. Pallet trucks help you lift heavy pallets and move them from one location to another. You can find these trucks in various types, like manual pallet trucks and electric pallet trucks. · These user-friendly trucks increase efficiency by removing the need for employees to have to depend on or wait for forklift trucks to move loads from one place to the other. With pallet trucks product can be safely and quickly moved so that space is made available for the next project at hand.
- Pallet stackers: When you need to stack, lift or move heavy pallets, pallet stackers should be at the top of your list. These machines are designed to fit in tight locations such as narrow racking aisles, making it easy for you to retrieve product from or place product onto your racks or shelves. Stackers can also be used to raise or lower pallets so that they can be loaded or unloaded at ergonomic heights that will provide safety and improved productivity for your workers.
- Drum lifters: If you work with chemicals or other hazardous materials, you likely have to handle drums in your day-to-day operations. Drum lifters are designed to handle these drums and transport them safely to the necessary locations. Since these machines eliminate the need for employees to move or lift drums by hand, you can save a significant amount of time and reduce the chances of employee injury.
- Industrial lift tables: When employees have to handle products by hand, their lifting, bending and reaching can all cause injuries. Lift tables reduce the amount of manual handling involved in palletizing or de-palletizing products at a warehouse. They can also be used to place pallets at an appropriate height for easy access. Adding lift tables to your warehouse can significantly impact your efficiency by making the load transfer process much faster and safer.
- Roller skids: Companies that need to move equipment and products from one place to another often turn to roller skids. These pieces of equipment can be used to move heavy machinery to areas in the warehouse where space is more confined and not easily accessible for forklift trucks. The construction and design of roller skids make them conducive for moving heavy loads within aisles or areas that require sharp turns. Whatever your rigging application roller skids are a great tool for efficiently getting the job done.
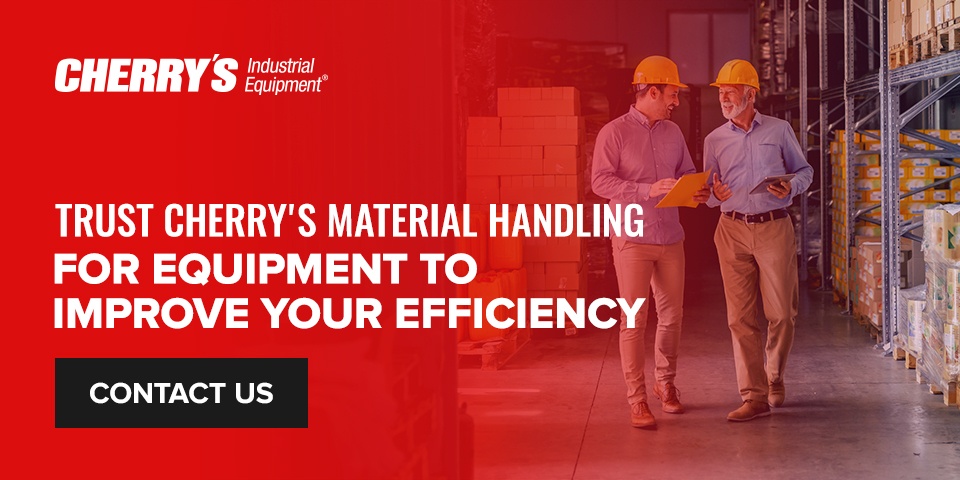
Trust Cherry’s Material Handling for Equipment to Improve Your Efficiency
Cherry’s Material Handling is ready to provide labor-saving equipment to improve your warehouse’s efficiency. We offer durable and powerful equipment to conduct tasks faster and reduce the need for physical labor. You can browse our selection of pallet trucks and carts today, as well as our ergonomic machinery, like lift tables, work positioners and drum lifters.
If you have any questions, contact us online or call 877-350-2729 to speak with one of our material handling representatives. Don’t see what you need for optimal efficiency? Don’t worry, we can build custom material handling solutions for your needs.